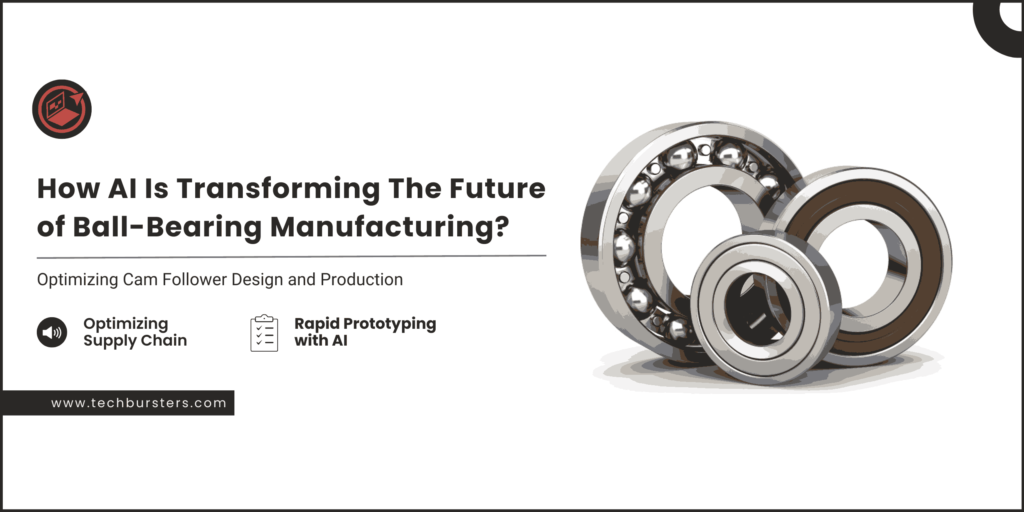
Imagine a factory floor buzzing with activity. Precision machinery works tirelessly to produce thousands of ball bearings each hour, essential components in everything from cars to wind turbines.
But despite the constant hum of production, something has changed—these machines are learning. Sensors monitor every aspect of the process, analyzing vibrations, temperatures, and speeds in real time, while AI-driven algorithms predict exactly when equipment will need maintenance, preventing costly breakdowns.
This is not science fiction; it’s the present.
According to a report, the global AI manufacturing market is expected to grow from $3.2 billion in 2023 to nearly $20.8 billion by 2028, driven by the demand for smart factories and automated processes.
In ball bearing manufacturing, AI is already transforming the industry by enhancing precision, reducing waste, and cutting costs. This article will explore how AI is not only reshaping current production methods but also laying the groundwork for innovations that will drive the future of the industry.
1. Optimizing Cam Follower Design and Production
The cam follower is a kind of roller or needle bearing that is extensively used in a wide variety of industries and for numerous purposes ranging from automotive engines to conveyors.
In the past, cam follower design and manufacturing were laborious and required a lot of calculations to ensure that the part would be able to handle significant load and also perform a rotational movement smoothly.
With simulation tools integrated via artificial intelligence, manufacturers can design cam followers that distribute the load, minimize friction, and enhance durability. This allows data from design, stress testing, and performance evaluation to suggest improvements or reveal some flaws before actual physical prototypes are developed.
This minimizes iteration in the design process, thus shortening product development cycles and producing higher-quality cam followers. Besides, manufacturing organizations have also incorporated AI-enabled robots in the making of cam followers, automating tasks like assembly, inspection of quality, and movement of materials.
This reduces errors that may be caused by human interventions during the production process and guarantees each cam follower meets the standards that are needed for particular industrial uses.
2. Enhancing Precision and Tolerance in Bearing Production
In ball bearing manufacturing, accuracy plays a central role. This is because bearings have to be manufactured with exacting tolerances to work effectively when rotating at high speeds or under large loads.
Any variation in the dimensions of a bearing, no matter how insignificant, can lead to higher friction, lower efficiency, and shorter life. Recent developments in AI are being employed to increase the degrees of accuracy and reliability in ball bearing making.
Real-time quality assurance is achieved with the help of machine vision and advanced sensors integrated into the system. These systems can identify minute imperfections or variations that a human eye cannot see.
Good to Read:- A Guide To Essential Windows Server Migration Tools
3. AI-Driven Predictive Maintenance for Production Equipment
Ball bearings are produced using very specialized manufacturing equipment, and any defect in such equipment is likely to result in a stoppage of production, leading to losses. In the past, maintenance processes were not proactive, and equipment was repaired only after a failure was detected.
However, AI is gradually moving the industry to predictive maintenance, which focuses on data analysis and machine learning to determine when a piece of equipment is likely to fail.
In addition to identifying machine failure signs, AI can also identify specific signs from sensor devices, such as increased temperature, variations in vibration, and other changes in power consumption.
These insights enable the maintenance teams to anticipate problems before they result in costly downtimes. It not only helps to increase the life expectancy of machinery but also guarantees no disruption of the production cycle, hence increasing efficiency and ultimately lowering costs.
4. Optimizing Supply Chain and Inventory Management
The ball bearing industry relies on the supply chain networks whereby the buyers and sellers of raw materials are supposed to coordinate with manufacturers and schedulers of the industry in replenishment of stocks and timely deliveries.
AI is particularly useful in supply chain management because it offers information about stock, usage rates and suppliers. As for potential future requirements for some specific types of bearings, AI algorithms study historical and current data processed to make evaluations.
This assists the manufacturers in strategizing the production of the products to meet the consumers’ demand without having to produce excess stock.
AI-driven systems can also assist in monitoring the stock of raw materials and order for some when the stock gets low, thereby reducing the incidence of production delays due to low stock of raw materials.
5. Customization and Rapid Prototyping with AI
The demand for custom ball bearings is rising because the aerospace, automotive, and robotics industries seek bearings suitable for their products. Fortunately, AI is helping manufacturers address these requirements by introducing fast prototyping and customization processes.
The design software powered by AI can generate precise virtual models of bearings corresponding to customers’ requirements. These models can be tested on AI-powered simulation platforms where the behavior of the bearing can be tested without the need for physical prototypes.
Also, AI can automate the process of customized bearing, ensuring the final product meets the required standards without significant human input. Such a level of customization is becoming more relevant in industries where efficiency, reliability, and performance are important.
Good to Read:- Compelling Press Release Example | Crafting Stories for Maximum Impact
Final Words
AI is now the leading technology that has led to an innovation shift within the ball-bearing manufacturing industry regarding the design, production, and testing of important elements.
That said, artificial intelligence is not merely a tool; it is evolving into an orchestration system that directs ways that enable more efficiency by forestalling challenges and refining processes in real-time. Furthermore, AI is building the groundwork for a more intelligent, adaptive, and efficient production process by boosting efficiency, lowering expenses, and improving quality assurance.
It is just a start, and thanks to AI, new performance standards are being opened that will set trends for years to come.